4H/6H-P 6inch SiC wafer Zero MPD grade Production Grade Dummy Grade
4H/6H-P Type SiC Composite Substrates Common parameter table
6 inch diameter Silicon Carbide (SiC) Substrate Specification
Grade | Zero MPD ProductionGrade (Z Grade) | Standard ProductionGrade (P Grade) | Dummy Grade (D Grade) | ||
Diameter | 145.5 mm~150.0 mm | ||||
Thickness | 350 μm ± 25 μm | ||||
Wafer Orientation | -Off axis: 2.0°-4.0°toward [1120] ± 0.5° for 4H/6H-P, On axis:〈111〉± 0.5° for 3C-N | ||||
Micropipe Density | 0 cm-2 | ||||
Resistivity | p-type 4H/6H-P | ≤0.1 Ωꞏcm | ≤0.3 Ωꞏcm | ||
n-type 3C-N | ≤0.8 mΩꞏcm | ≤1 m Ωꞏcm | |||
Primary Flat Orientation | 4H/6H-P | -{1010} ± 5.0° | |||
3C-N | -{110} ± 5.0° | ||||
Primary Flat Length | 32.5 mm ± 2.0 mm | ||||
Secondary Flat Length | 18.0 mm ± 2.0 mm | ||||
Secondary Flat Orientation | Silicon face up: 90° CW. from Prime flat ± 5.0° | ||||
Edge Exclusion | 3 mm | 6 mm | |||
LTV/TTV/Bow /Warp | ≤2.5 μm/≤5 μm/≤15 μm/≤30 μm | ≤10 μm/≤15 μm/≤25 μm/≤40 μm | |||
Roughness | Polish Ra≤1 nm | ||||
CMP Ra≤0.2 nm | Ra≤0.5 nm | ||||
Edge Cracks By High Intensity Light | None | Cumulative length ≤ 10 mm, single length≤2 mm | |||
Hex Plates By High Intensity Light | Cumulative area ≤0.05% | Cumulative area ≤0.1% | |||
Polytype Areas By High Intensity Light | None | Cumulative area≤3% | |||
Visual Carbon Inclusions | Cumulative area ≤0.05% | Cumulative area ≤3% | |||
Silicon Surface Scratches By High Intensity Light | None | Cumulative length≤1×wafer diameter | |||
Edge Chips High By Intensity Light | None permitted ≥0.2mm width and depth | 5 allowed, ≤1 mm each | |||
Silicon Surface Contamination By High Intensity | None | ||||
Packaging | Multi-wafer Cassette or Single Wafer Container |
Notes:
※ Defects limits apply to entire wafer surface except for the edge exclusion area. # The scratches should be checked on Si face o
The 4H/6H-P type 6-inch SiC wafer with Zero MPD grade and production or dummy grade is widely used in advanced electronic applications. Its excellent thermal conductivity, high breakdown voltage, and resistance to harsh environments make it ideal for power electronics, such as high-voltage switches and inverters. The Zero MPD grade ensures minimal defects, critical for high-reliability devices. Production-grade wafers are used in large-scale manufacturing of power devices and RF applications, where performance and precision are crucial. Dummy-grade wafers, on the other hand, are used for process calibration, equipment testing, and prototyping, enabling consistent quality control in semiconductor production environments.
The advantages of N-type SiC composite substrates include
- High Thermal Conductivity: The 4H/6H-P SiC wafer efficiently dissipates heat, making it suitable for high-temperature and high-power electronic applications.
- High Breakdown Voltage: Its ability to handle high voltages without failure makes it ideal for power electronics and high-voltage switching applications.
- Zero MPD (Micro Pipe Defect) Grade: Minimal defect density ensures higher reliability and performance, critical for demanding electronic devices.
- Production-Grade for Mass Manufacturing: Suitable for large-scale production of high-performance semiconductor devices with stringent quality standards.
- Dummy-Grade for Testing and Calibration: Enables process optimization, equipment testing, and prototyping without using high-cost production-grade wafers.
Overall, 4H/6H-P 6-inch SiC wafers with Zero MPD grade, production grade, and dummy grade offer significant advantages for the development of high-performance electronic devices. These wafers are particularly beneficial in applications requiring high-temperature operation, high power density, and efficient power conversion. The Zero MPD grade ensures minimal defects for reliable and stable device performance, while the production-grade wafers support large-scale manufacturing with strict quality controls. Dummy-grade wafers provide a cost-effective solution for process optimization and equipment calibration, making them indispensable for high-precision semiconductor fabrication.
Detailed Diagram
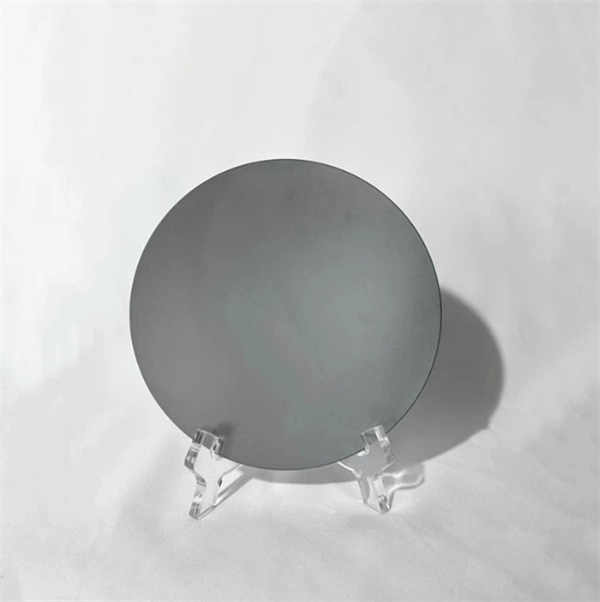
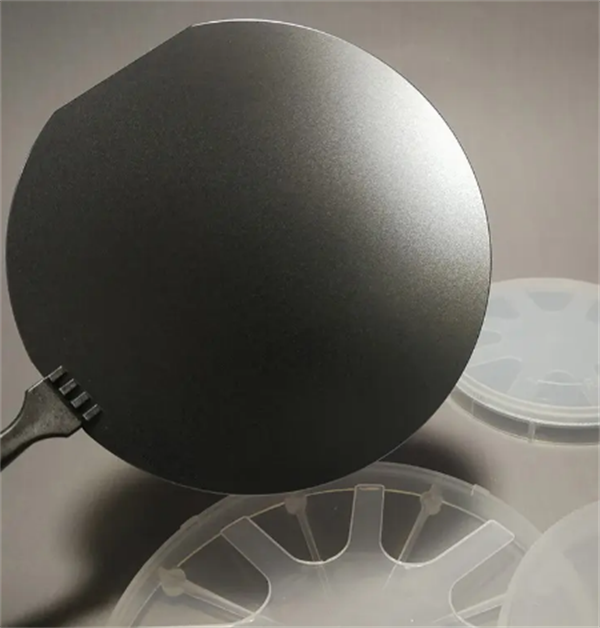