Au coated wafer,sapphire wafer,silicon wafer,SiC wafer ,2inch 4inch 6inch,Gold coated thickeness 10nm 50nm 100nm
Key Features
Feature |
Description |
Substrate Materials | Silicon (Si), Sapphire (Al₂O₃), Silicon Carbide (SiC) |
Gold Coating Thickness | 10nm, 50nm, 100nm, 500nm |
Gold Purity | 99.999% purity for optimal performance |
Adhesion Film | Chromium (Cr), 99.98% purity, ensuring strong adhesion |
Surface Roughness | Several nm (smooth surface quality for precision applications) |
Resistance (Si Wafer) | 1-30 Ohm/cm (depending on type) |
Wafer Sizes | 2-inch, 4-inch, 6-inch, and custom sizes |
Thickness (Si Wafer) | 275µm, 381µm, 525µm |
TTV (Total Thickness Variation) | ≤ 20µm |
Primary Flat (Si Wafer) | 15.9 ± 1.65mm to 32.5 ± 2.5mm |
Why Gold Coating is Essential in the Semiconductor Industry
Electrical Conductivity
Gold is one of the best materials for electrical conduction. Gold-coated wafers provide low-resistance pathways, which are essential for semiconductor devices that require fast and stable electrical connections. The high purity of gold ensures optimal conductivity, minimizing signal loss.
Corrosion Resistance
Gold is non-corrosive and highly resistant to oxidation. This makes it ideal for semiconductor applications that operate in harsh environments or are subject to high temperatures, moisture, or other corrosive conditions. A gold-coated wafer will maintain its electrical properties and reliability over time, providing a long service life for the devices in which it is used.
Thermal Management
Gold's excellent thermal conductivity ensures that the heat generated during the operation of semiconductor devices is dissipated efficiently. This is particularly important for high-power applications like LEDs, power electronics, and optoelectronic devices, where excess heat can lead to device failure if not properly managed.
Mechanical Durability
Gold coatings provide mechanical protection to the wafer, preventing surface damage during handling and processing. This added layer of protection ensures that wafers retain their structural integrity and reliability, even in demanding conditions.
Post-Coating Characteristics
Enhanced Surface Quality
The gold coating improves the surface smoothness of the wafer, which is crucial for high-precision applications. The surface roughness is minimized to several nanometers, ensuring a flawless surface ideal for processes such as wire bonding, soldering, and photolithography.
Improved Bonding and Soldering Properties
The gold layer enhances the bonding properties of the wafer, making it ideal for wire bonding and flip-chip bonding. This results in secure and long-lasting electrical connections in IC packaging and semiconductor assemblies.
Corrosion-Free and Long-lasting
The gold coating ensures that the wafer will remain free from oxidation and degradation, even after prolonged exposure to harsh environmental conditions. This contributes to the long-term stability of the final semiconductor device.
Thermal and Electrical Stability
Gold-coated wafers provide consistent thermal dissipation and electrical conductivity, leading to better performance and reliability of the devices over time, even in extreme temperatures.
Parameters
Property |
Value |
Substrate Materials | Silicon (Si), Sapphire (Al₂O₃), Silicon Carbide (SiC) |
Gold Layer Thickness | 10nm, 50nm, 100nm, 500nm |
Gold Purity | 99.999% (high purity for optimal performance) |
Adhesion Film | Chromium (Cr), 99.98% purity |
Surface Roughness | Several nanometers |
Resistance (Si Wafer) | 1-30 Ohm/cm |
Wafer Sizes | 2-inch, 4-inch, 6-inch, custom sizes |
Si Wafer Thickness | 275µm, 381µm, 525µm |
TTV | ≤ 20µm |
Primary Flat (Si Wafer) | 15.9 ± 1.65mm to 32.5 ± 2.5mm |
Applications of Gold-Coated Wafers
Semiconductor Packaging
Gold-coated wafers are extensively used in IC packaging, where their electrical conductivity, mechanical durability, and thermal dissipation properties ensure reliable interconnects and bonding in semiconductor devices.
LED Manufacturing
Gold-coated wafers play a critical role in LED manufacturing, where they enhance thermal management and electrical performance. The gold layer ensures that the heat generated by high-power LEDs is dissipated efficiently, contributing to longer lifespan and better efficiency.
Optoelectronic Devices
In optoelectronics, gold-coated wafers are used in devices like photodetectors, laser diodes, and light sensors. The gold coating provides excellent thermal conductivity and electrical stability, ensuring consistent performance in devices that require precise control of light and electrical signals.
Power Electronics
Gold-coated wafers are essential for power electronic devices, where high efficiency and reliability are crucial. These wafers ensure stable power conversion and heat dissipation in devices such as power transistors and voltage regulators.
Microelectronics and MEMS
In microelectronics and MEMS (Micro-Electromechanical Systems), gold-coated wafers are used to create microelectromechanical components that require high precision and durability. The gold layer provides stable electrical performance and mechanical protection in sensitive microelectronic devices.
Frequently Asked Questions (Q&A)
Q1: Why use gold for coating wafers?
A1: Gold is used for its superior electrical conductivity, corrosion resistance, and thermal management properties. It ensures reliable interconnects, longer device lifespan, and consistent performance in semiconductor applications.
Q2: What are the benefits of using gold-coated wafers in semiconductor applications?
A2: Gold-coated wafers provide high reliability, long-term stability, and better electrical and thermal performance. They also enhance bonding properties and protect against oxidation and corrosion.
Q3: What thickness of gold coating should I choose for my application?
A3: The ideal thickness depends on your specific application. 10nm is suitable for precise, delicate applications, while 50nm to 100nm coatings are used for higher power devices. 500nm may be used for heavy-duty applications requiring thicker layers for durability and heat dissipation.
Q4: Can you customize the wafer sizes?
A4: Yes, wafers are available in 2-inch, 4-inch, and 6-inch standard sizes, and we can also provide custom sizes to meet your specific requirements.
Q5: How does the gold coating enhance device performance?
A5: Gold improves thermal dissipation, electrical conductivity, and corrosion resistance, all of which contribute to more efficient and reliable semiconductor devices with longer operational lifetimes.
Q6: How does the adhesion film improve the gold coating?
A6: The chromium (Cr) adhesion film ensures a strong bond between the gold layer and the substrate, preventing delamination and ensuring the integrity of the wafer during processing and use.
Conclusion
Our Gold Coated Silicon, Sapphire, and SiC Wafers offer advanced solutions for semiconductor applications, providing superior electrical conductivity, thermal dissipation, and corrosion resistance. These wafers are ideal for semiconductor packaging, LED manufacturing, optoelectronics, and more. With high-purity gold, customizable coating thickness, and excellent mechanical durability, they ensure long-term reliability and consistent performance in demanding environments.
Detailed Diagram
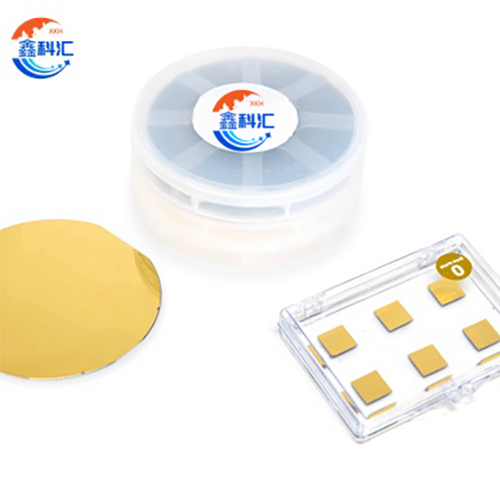
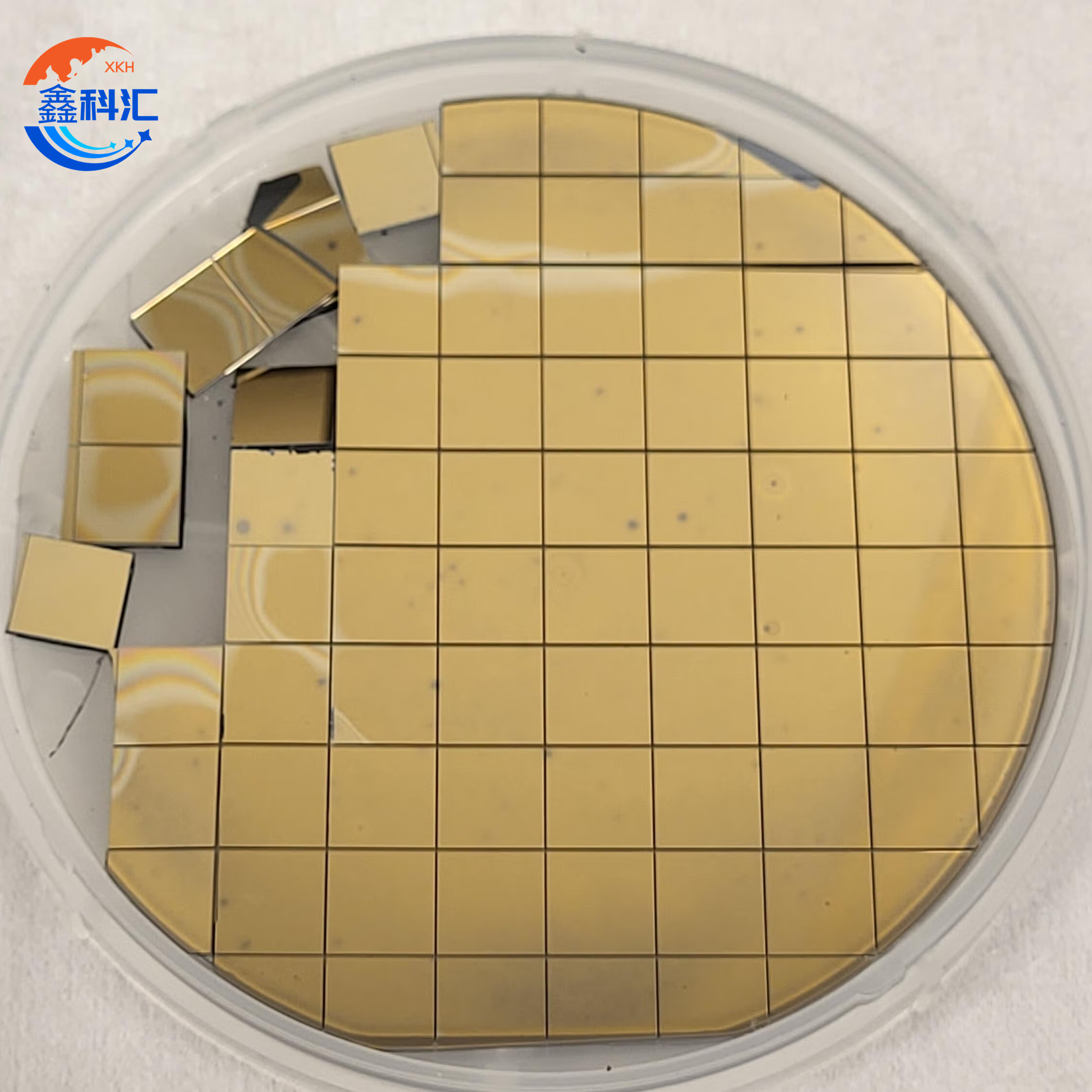
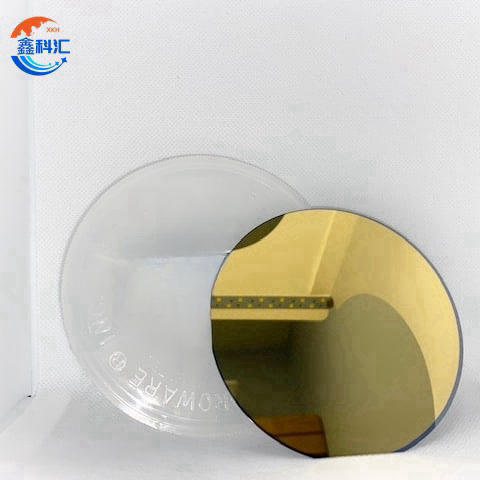
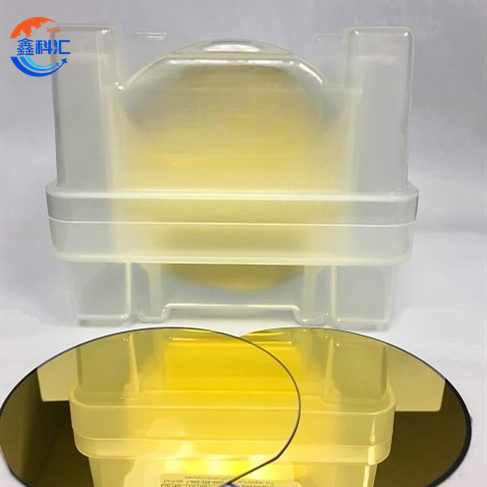