Customizable Silicon Carbide Ceramic Tray with CVD SiC Coating for High-Temperature Sintering and Chemical Processing – High Strength and Durability
Features
1.High Thermal Stability: With a maximum working temperature of 1500°C, the trays can withstand extreme heat, making them ideal for high-temperature sintering processes in ceramics and materials manufacturing.
2.CVD SiC Coating: The CVD SiC coating enhances the tray’s thermal shock resistance, wear resistance, and chemical durability, ensuring extended service life even in harsh environments.
3.Customizable Size and Shape: The trays can be tailored to meet specific requirements, providing flexibility for various applications and ensuring perfect compatibility with equipment.
4.High Mechanical Strength: Silicon carbide’s exceptional mechanical properties, including flexural strength and compressive strength, ensure that the trays can support heavy loads and withstand mechanical stresses.
5.Chemical Resistance: These trays are highly resistant to aggressive chemicals, making them ideal for use in chemical processing, reaction vessels, and distillation columns.
6.Low Thermal Expansion: With a low coefficient of thermal expansion, these trays maintain dimensional stability and reduce the risk of warping or cracking when subjected to temperature fluctuations.
Applications
●High-Temperature Sintering: These trays are widely used in advanced ceramics production for sintering high-performance materials such as ceramic composites and metals, which require precise heat management.
●Semiconductor Manufacturing: The trays support silicon wafers and other sensitive materials during various semiconductor fabrication processes, including epitaxy, diffusion, and oxidation.
●Chemical Processing: Due to their high chemical resistance, the trays are ideal for handling corrosive substances in chemical reactors and distillation systems, ensuring safe and efficient material processing.
●Aerospace and Automotive: Used in aerospace components and automotive manufacturing, these trays offer thermal resistance, lightweight properties, and strength necessary for advanced material processing.
●Optical Component Manufacturing: In optical systems, where precise temperature control is essential, these trays are used for material sintering and component manufacturing.
Product Parameters
Feature |
Specification |
Material | Silicon Carbide (SiC), CVD SiC Coating |
Density | 3.12g/cm³ |
Hardness | ≥92 HRA |
Thermal Conductivity | 110 W/m·K |
Flexural Strength | 359 MPa |
Compressive Strength | ≥2200 MPa |
Max. Working Temperature | 1500°C |
Coefficient of Thermal Expansion | 4.0 x 10^-6/°C |
Applications | Semiconductor, Chemical Processing, High-Temperature Sintering |
Customization | Available in Custom Sizes and Shapes |
Q&A (Frequently Asked Questions)
Q1: What is the advantage of the CVD SiC coating on these ceramic trays?
A1: The CVD SiC coating improves the tray’s thermal shock resistance, wear resistance, and chemical resistance, making it suitable for use in harsh environments where untreated materials would degrade or fail.
Q2: How high a temperature can these trays handle?
A2: These trays can withstand temperatures up to 1500°C, making them ideal for high-temperature sintering and other applications that involve extreme heat.
Q3: Can I customize the size and shape of these trays?
A3: Yes, these trays can be customized to meet the specific needs of your application, with options for different sizes, shapes, and thicknesses.
Q4: How does the low coefficient of thermal expansion benefit these trays?
A4: A low coefficient of thermal expansion ensures that the trays maintain dimensional stability when subjected to temperature fluctuations, reducing the risk of warping or cracking.
Q5: What are some common industries that use silicon carbide ceramic trays?
A5: These trays are commonly used in semiconductor manufacturing, chemical processing, aerospace, and automotive industries due to their thermal stability, strength, and chemical resistance.
Detailed Diagram
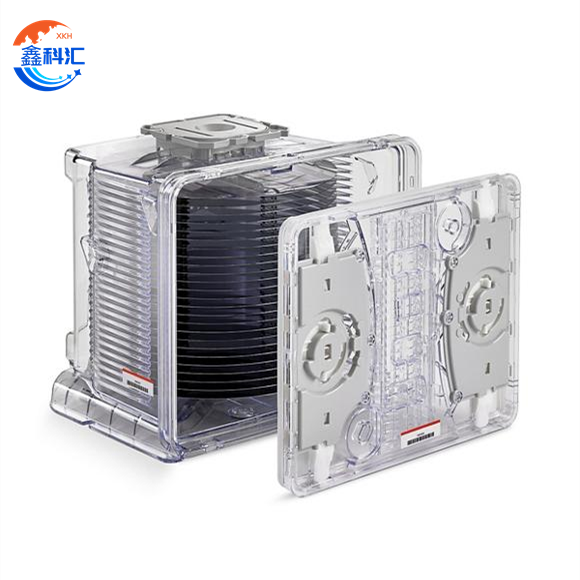
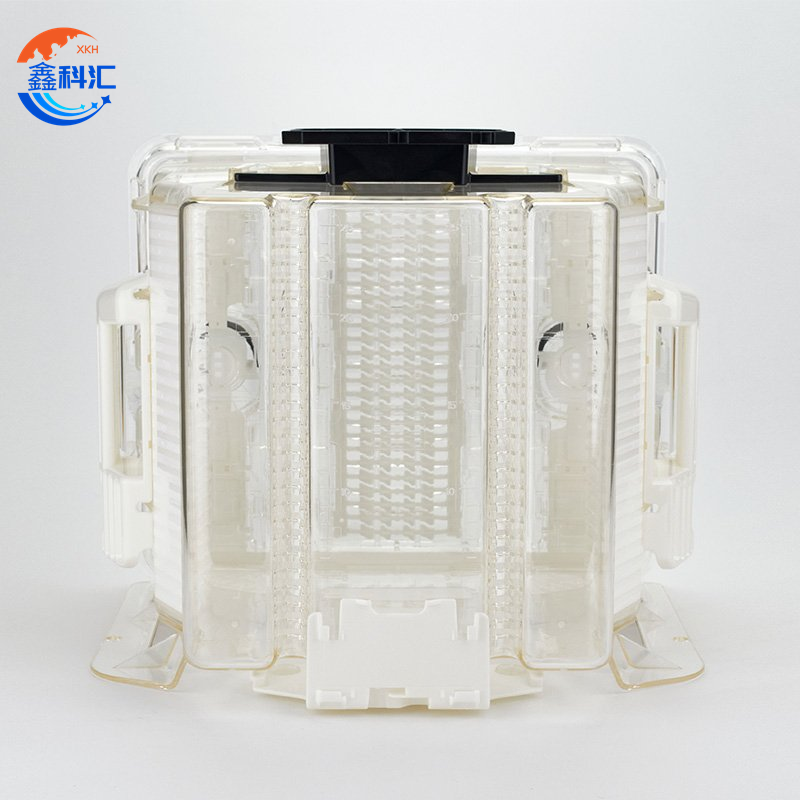
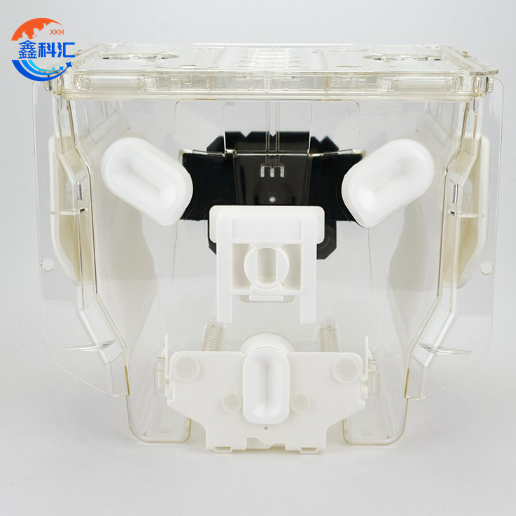
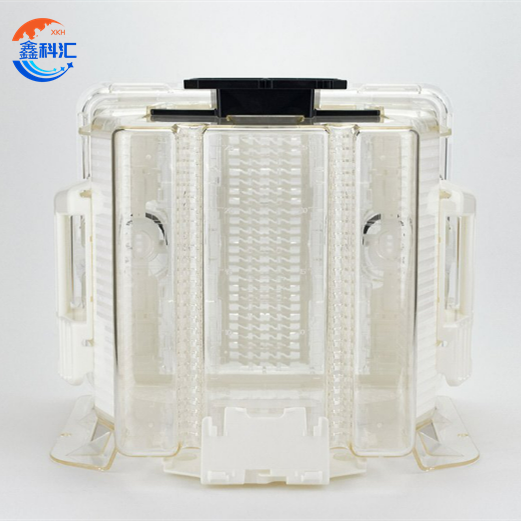