CVD method for producing high purity SiC raw materials in silicon carbide synthesis furnace at 1600℃
Working principle:
1. Precursor supply. Silicon source (e.g. SiH₄) and carbon source (e.g. C₃H₈) gases are mixed in proportion and fed into the reaction chamber.
2. High temperature decomposition: At a high temperature of 1500~2300℃, the gas decomposition generates Si and C active atoms.
3. Surface reaction: Si and C atoms are deposited on the substrate surface to form a SiC crystal layer.
4. Crystal growth: Through the control of temperature gradient, gas flow and pressure, to achieve directional growth along the c axis or the a axis.
Key parameters:
· Temperature: 1600~2200℃ (>2000℃ for 4H-SiC)
· Pressure: 50~200mbar (low pressure to reduce gas nucleation)
· Gas ratio: Si/C≈1.0~1.2 (to avoid Si or C enrichment defects)
Main features:
(1) Crystal quality
Low defect density: microtubule density < 0.5cm ⁻², dislocation density <10⁴ cm⁻².
Polycrystalline type control: can grow 4H-SiC (mainstream), 6H-SiC, 3C-SiC and other crystal types.
(2) Equipment performance
High temperature stability: graphite induction heating or resistance heating, temperature >2300℃.
Uniformity control: temperature fluctuation ±5℃, growth rate 10~50μm/h.
Gas system: High precision mass flowmeter (MFC), gas purity ≥99.999%.
(3) Technological advantages
High purity: Background impurity concentration <10¹⁶ cm⁻³ (N, B, etc.).
Large sizing: Support 6 "/8" SiC substrate growth.
(4) Energy consumption and cost
High energy consumption (200~500kW·h per furnace), accounting for 30%~50% of the production cost of SiC substrate.
Core applications:
1. Power semiconductor substrate: SiC MOSFETs for manufacturing electric vehicles and photovoltaic inverters.
2. Rf device: 5G base station GaN-on-SiC epitaxial substrate.
3.Extreme environment devices: high temperature sensors for aerospace and nuclear power plants.
Technical specification:
Specification | Details |
Dimensions (L × W × H) | 4000 x 3400 x 4300 mm or customize |
Furnace chamber diameter | 1100mm |
Loading capacity | 50kg |
The limit vacuum degree | 10-2Pa(2h after the molecular pump starts) |
Chamber pressure rise rate | ≤10Pa/h(after calcination) |
Lower furnace cover lifting stroke | 1500mm |
Heating method | Induction heating |
The maximum temperature in the furnace | 2400°C |
Heating power supply | 2X40kW |
Temperature measurement | Two-color infrared temperature measurement |
Temperature range | 900~3000℃ |
Temperature control accuracy | ±1°C |
Control pressure range | 1~700mbar |
Pressure Control Accuracy | 1~5mbar ±0.1mbar; 5~100mbar ±0.2mbar; 100~700mbar ±0.5mbar |
Loading method | Lower loading; |
Optional configuration | Double temperature measuring point, unloading forklift. |
XKH Services:
XKH provides full-cycle services for silicon carbide CVD furnaces, including equipment customization (temperature zone design, gas system configuration), process development (crystal control, defect optimization), technical training (operation and maintenance) and after-sales support (spare parts supply of key components, remote diagnosis) to help customers achieve high-quality SiC substrate mass production. And provide process upgrade services to continuously improve crystal yield and growth efficiency.
Detailed Diagram
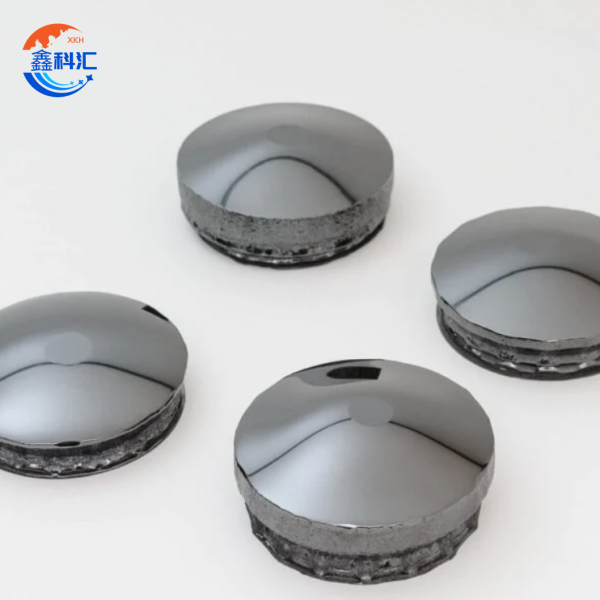
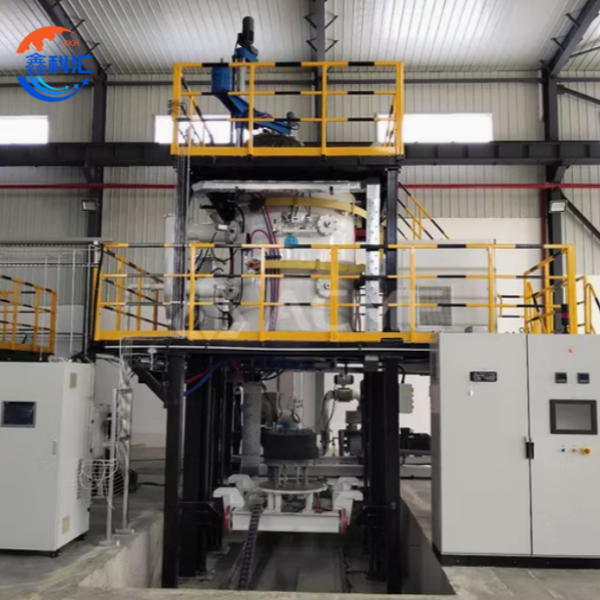
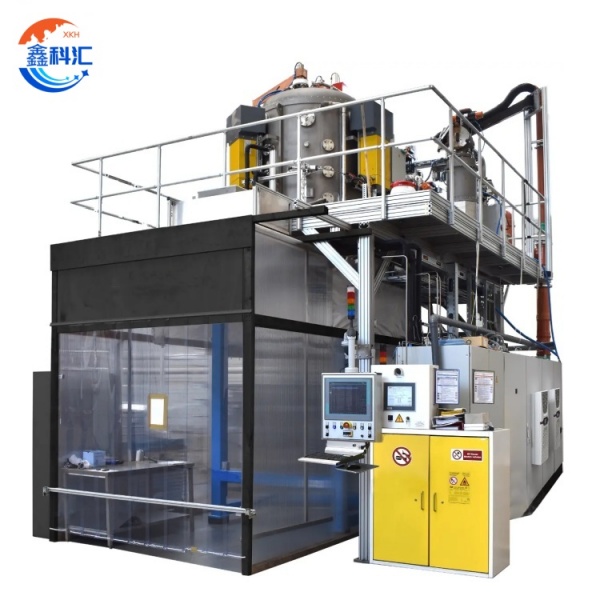