Double station square machine monocrystalline silicon rod processing 6/8/12 inch surface flatness Ra≤0.5μm
Equipment characteristics:
(1) Double station synchronous processing
· Double efficiency: Simultaneous processing of two silicon rods (Ø6"-12") increases productivity by 40%-60% vs. Simplex equipment.
· Independent control: Each station can independently adjust the cutting parameters (tension, feed speed) to adapt to different silicon rod specifications.
(2) High-precision cutting
· Dimensional accuracy: square bar side distance tolerance ±0.15mm, range ≤0.20mm.
· Surface quality: cutting edge breakage <0.5mm, reduce the amount of subsequent grinding.
(3) Intelligent control
· Adaptive cutting: real-time monitoring of silicon rod morphology, dynamic adjustment of cutting path (such as processing bent silicon rod).
· Data traceability: record the processing parameters of each silicon rod to support MES system docking.
(4) Low consumable cost
· Diamond wire consumption: ≤0.06m/mm (silicon rod length), wire diameter ≤0.30mm.
· Coolant circulation: The filtration system extends the service life and reduces waste liquid disposal.
Technology and development advantages:
(1) Cutting technology optimization
- Multi-line cutting: 100-200 diamond lines are used in parallel, and the cutting speed is ≥40mm/min.
- Tension control: Closed loop adjustment system (±1N) to reduce the risk of wire breakage.
(2) Compatibility extension
- Material adaptation: Support P-type/N-type monocrystalline silicon, compatible with TOPCon, HJT and other high-efficiency battery silicon rods.
- Flexible size: silicon rod length 100-950mm, square rod side distance 166-233mm adjustable.
(3) Automation upgrade
- Robot loading and unloading: automatic loading/unloading of silicon rods, beat ≤3 minutes.
- Intelligent diagnostics: Predictive maintenance to reduce unplanned downtime.
(4) Industry leadership
- Wafer support: can process ≥100μm ultra-thin silicon with square rods, fragmentation rate <0.5%.
- Energy consumption optimization: Energy consumption per unit of silicon rod is reduced by 30% (vs. traditional equipment).
Technical parameters:
Name of parameter | Index value |
Number of bars processed | 2 pieces/set |
Processing bar length range | 100~950mm |
Machining margin range | 166~233mm |
Cutting speed | ≥40mm/min |
Diamond wire speed | 0~35m/s |
Diamond diameter | 0.30 mm or less |
Linear consumption | 0.06 m/mm or less |
Compatible round rod diameter | Finished square rod diameter +2mm, Ensure polishing pass rate |
Cutting edge breakage control | Raw edge ≤0.5mm, No chipping, high surface quality |
Arc length uniformity | Projection range <1.5mm, Except for silicon rod distortion |
Machine dimensions (single machine) | 4800×3020×3660mm |
Total rated power | 56kW |
Dead weight of equipment | 12t |
Machining accuracy index table:
Precision item | Tolerance range |
Square bar margin tolerance | ±0.15mm |
Square bar edge range | ≤0.20mm |
Angle on all sides of square rod | 90°±0.05° |
Flatness of square rod | ≤0.15mm |
Robot repeated positioning accuracy | ±0.05mm |
XKH's services:
XKH provides full-cycle services for mono-crystalline silicon dual-station machines, including equipment customization (compatible with large silicon rods), process commissioning (cutting parameter optimization), operational training and after-sales support (key parts supply, remote diagnosis), ensuring that customers achieve high yield (>99%) and low consumable cost production, and providing technical upgrades (such as AI cutting optimization). The delivery period is 2-4 months.
Detailed Diagram
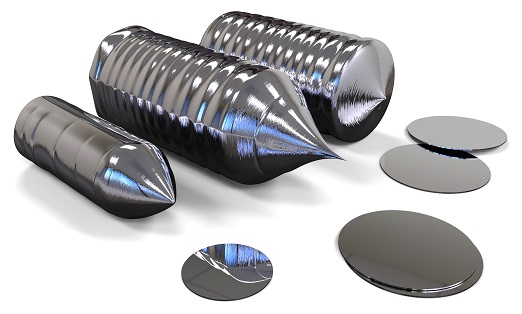
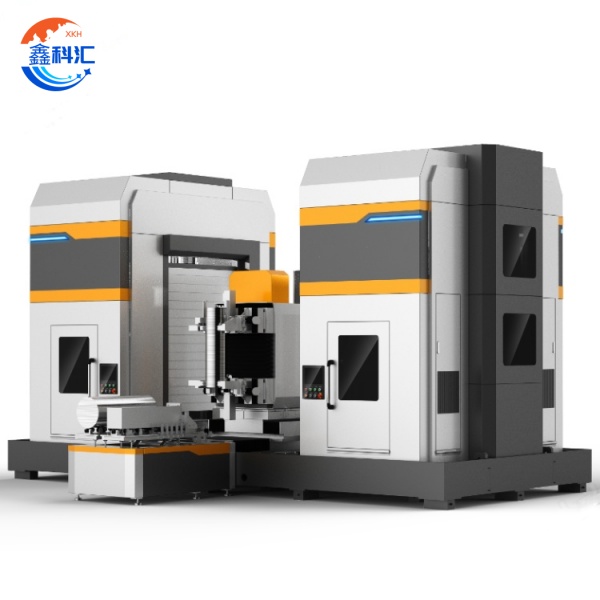
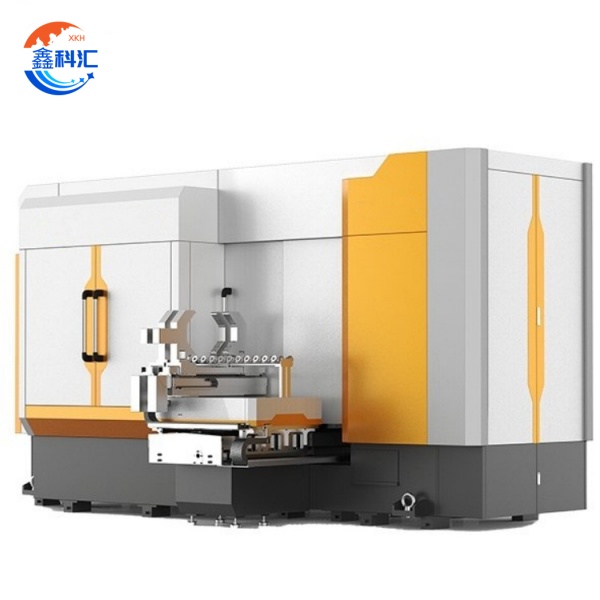
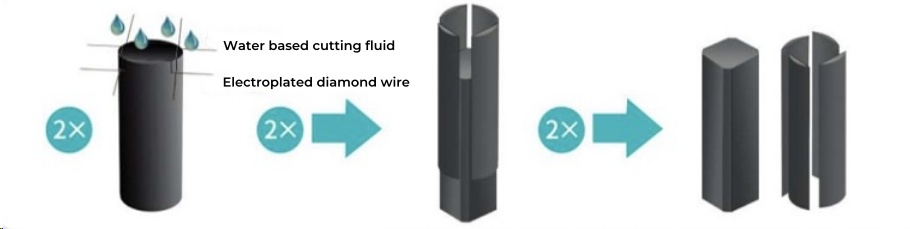