High precision laser drilling machine for sapphire ceramic material gem bearing nozzle drilling
Product Introduction
Applicable materials: Suitable for natural steel, polycrystalline steel, ruby, sapphire, copper, ceramics, rhenium, stainless steel, carbon steel, alloy steel and other superhard, high temperature resistant materials for different shapes, diameters, depths and taper drilling.
Working conditions
1. It is suitable for operation under the ambient temperature of 18℃-28℃ and relative humidity of 30%-60%.
2. Suitable for two-phase power supply /220V/50HZ/10A.
3. Configure plugs that meet the requirements of the relevant Chinese standards. If there is no such plug, an appropriate adapter should be provided.
4. Widely used in diamond wire drawing die, slow wire die, muffler hole, needle hole, gem bearing, nozzle and other perforating industries.
Technical parameters
Name | Data | Function |
Optical maser wavelength | 354.7nm or 355nm | Determines the energy distribution and penetration capacity of the laser beam, and affects the material absorption rate and processing effect. |
Average output power | 10.0 / 12.0/15.0 w@40khz | Affect the processing efficiency and punching speed, the higher the power, the faster the processing speed. |
Pulse width | Less than 20ns@40KHz | The short pulse width reduces the heat affected zone, improves the machining accuracy, and avoids the thermal damage of the material. |
Pulse repetition rate | 10~200KHz | Determine the transmission frequency and punching efficiency of the laser beam, the higher the frequency, the faster the punching speed. |
optical beam quality | M²<1.2 | High quality beams ensure drilling accuracy and edge quality, reducing energy loss. |
Spot diameter | 0.8±0.1mm | Determine the minimum aperture and machining accuracy, the smaller the spot, the smaller the aperture, the higher the accuracy. |
beam-divergence angle | Greater than 90% | The focusing ability and punching depth of the laser beam are affected. The smaller the divergence Angle, the stronger the focusing ability. |
Beam ellipticity | Less than 3% RMS | The smaller the ellipticity, the closer the shape of the hole is to the circle, the higher the machining accuracy. |
Processing capacity
High-precision laser drilling machines have powerful processing capabilities and can drill holes from a few microns to a few millimeters in diameter, and the shape, size, position and Angle of the holes can be precisely controlled. At the same time, the equipment supports 360-degree all-round drilling, which can meet the drilling needs of various complex shapes and structures. In addition, the high precision laser punching machine also has excellent edge quality and surface finish, the processed holes are burr free, no edge melting, and the hole surface is smooth and flat.
Application of high precision laser punching machine:
1. Electronics industry:
Printed circuit board (PCB) : used for microhole processing to meet the needs of high-density interconnection.
Semiconductor packaging: Punch holes in wafers and packaging materials to improve package density and performance.
2. Aerospace:
Engine blade cooling holes: Micro cooling holes are machined on superalloy blades to improve engine efficiency.
Composite processing: For high-precision drilling of carbon fiber composites to ensure structural strength.
3. Medical Equipment:
Minimally invasive surgical instruments: Machining microholes in surgical instruments to improve accuracy and safety.
Drug delivery system: Punch holes in the drug delivery device to control the drug release rate.
4. Automobile Manufacturing:
Fuel injection system: Machining micro-holes on the fuel injection nozzle to optimize the fuel atomization effect.
Sensor manufacturing: Drilling holes in the sensor element to improve its sensitivity and response speed.
5. Optical devices:
Optical fiber connector: Machining microholes on the optical fiber connector to ensure the quality of signal transmission.
Optical filter: Punch holes in the optical filter to achieve specific wavelength selection.
6. Precision machinery:
Precision mold: Machining microholes on the mold to improve the performance and service life of the mold.
Micro parts: Punch holes on the micro parts to meet the needs of high-precision assembly.
XKH provides a full range of high-precision laser drilling machine services, including equipment sales, technical support, customized solutions, installation and commissioning, operation training and after-sales maintenance, etc., to ensure that customers in the use of professional, efficient and comprehensive support.
Detailed Diagram
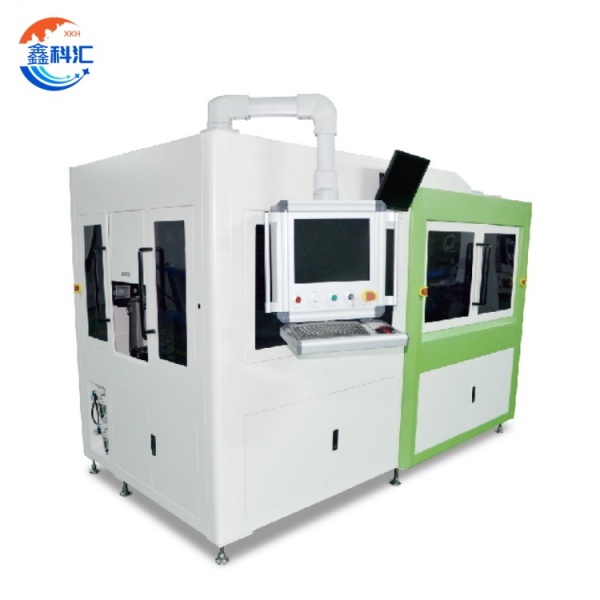

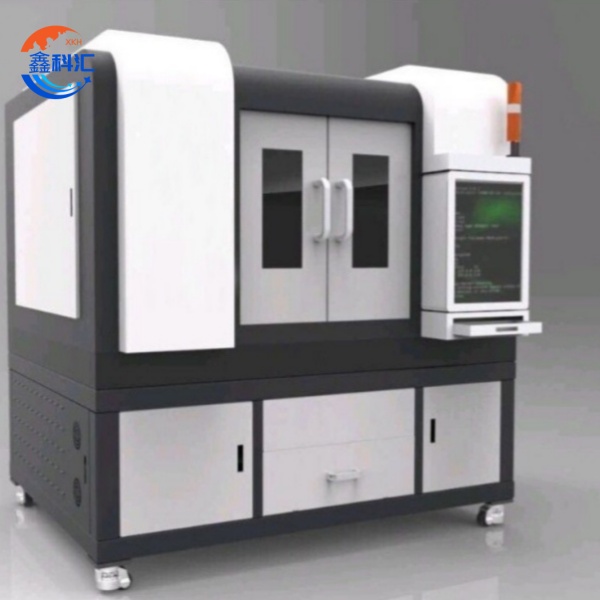