Microjet laser technology equipment wafer cutting SiC material processing
Working principle:
1. Laser coupling: pulsed laser (UV/green/infrared) is focused inside the liquid jet to form a stable energy transmission channel.
2. Liquid guidance: high-speed jet (flow rate 50-200m/s) cooling the processing area and taking away debris to avoid heat accumulation and pollution.
3. Material removal: The laser energy causes cavitation effect in the liquid to achieve cold processing of the material (heat affected zone <1μm).
4. Dynamic control: real-time adjustment of laser parameters (power, frequency) and jet pressure to meet the needs of different materials and structures.
Key parameters:
1. Laser power: 10-500W (adjustable)
2. Jet diameter: 50-300μm
3.Machining accuracy: ±0.5μm (cutting), depth to width ratio 10:1 (drilling)
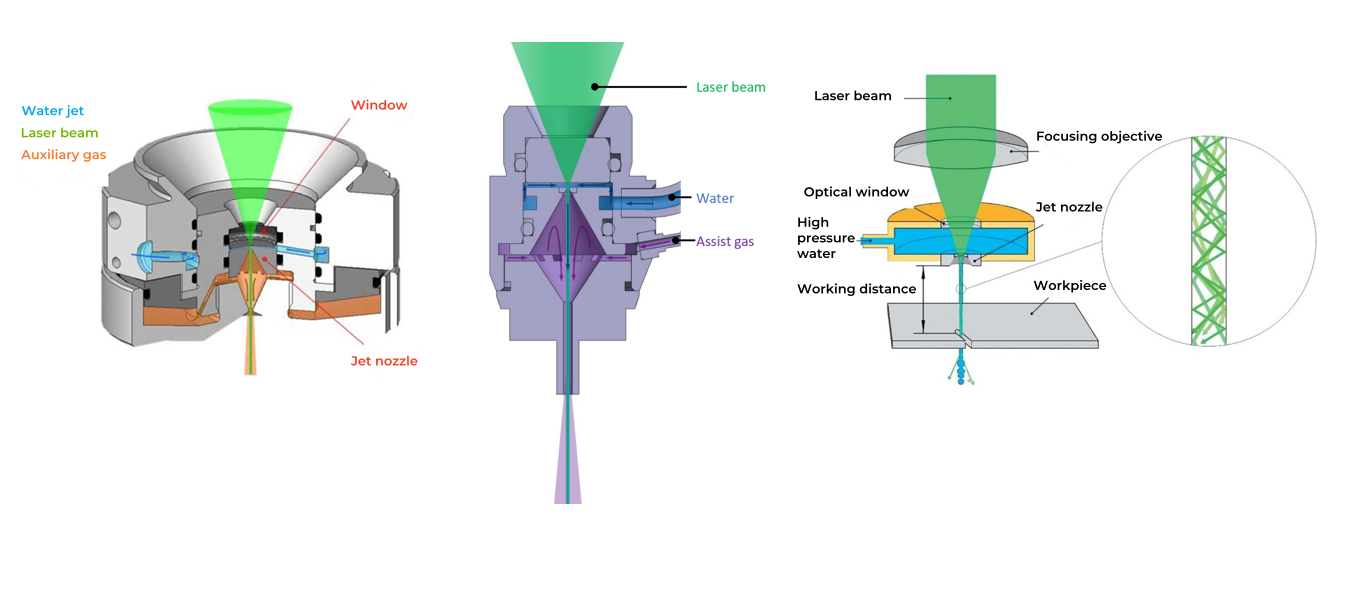
Technical advantages:
(1) Almost zero heat damage
- Liquid jet cooling controls the heat affected zone (HAZ) to **<1μm**, avoiding micro-cracks caused by conventional laser processing (HAZ is usually >10μm).
(2) Ultra-high precision machining
- Cutting/drilling accuracy up to **±0.5μm**, edge roughness Ra<0.2μm, reduce the need for subsequent polishing.
- Support complex 3D structure processing (such as conical holes, shaped slots).
(3) Wide material compatibility
- Hard and brittle materials: SiC, sapphire, glass, ceramics (traditional methods are easy to shatter).
- Heat sensitive materials: polymers, biological tissues (no risk of thermal denaturation).
(4) Environmental protection and efficiency
- No dust pollution, liquid can be recycled and filtered.
- 30%-50% increase in processing speed (vs. machining).
(5) Intelligent control
- Integrated visual positioning and AI parameter optimization, adaptive material thickness and defects.
Technical specifications:
Countertop volume | 300*300*150 | 400*400*200 |
Linear axis XY | Linear motor. Linear motor | Linear motor. Linear motor |
Linear axis Z | 150 | 200 |
Positioning accuracy μm | +/-5 | +/-5 |
Repeated positioning accuracy μm | +/-2 | +/-2 |
Acceleration G | 1 | 0.29 |
Numerical control | 3 axis /3+1 axis /3+2 axis | 3 axis /3+1 axis /3+2 axis |
Numerical control type | DPSS Nd:YAG | DPSS Nd:YAG |
Wavelength nm | 532/1064 | 532/1064 |
Rated power W | 50/100/200 | 50/100/200 |
Water jet | 40-100 | 40-100 |
Nozzle pressure bar | 50-100 | 50-600 |
Dimensions (machine tool) (width * length * height) mm | 1445*1944*2260 | 1700*1500*2120 |
Size (control cabinet) (W * L * H) | 700*2500*1600 | 700*2500*1600 |
Weight (equipment) T | 2.5 | 3 |
Weight (control cabinet) KG | 800 | 800 |
Processing capability | Surface roughness Ra≤1.6um
Opening speed ≥1.25mm/s Circumference cutting ≥6mm/s Linear cutting speed ≥50mm/s |
Surface roughness Ra≤1.2um
Opening speed ≥1.25mm/s Circumference cutting ≥6mm/s Linear cutting speed ≥50mm/s |
For gallium nitride crystal, ultra-wide band gap semiconductor materials (diamond/Gallium oxide), aerospace special materials, LTCC carbon ceramic substrate, photovoltaic, scintillator crystal and other materials processing. Note: Processing capacity varies depending on material characteristics
|
Processing case:
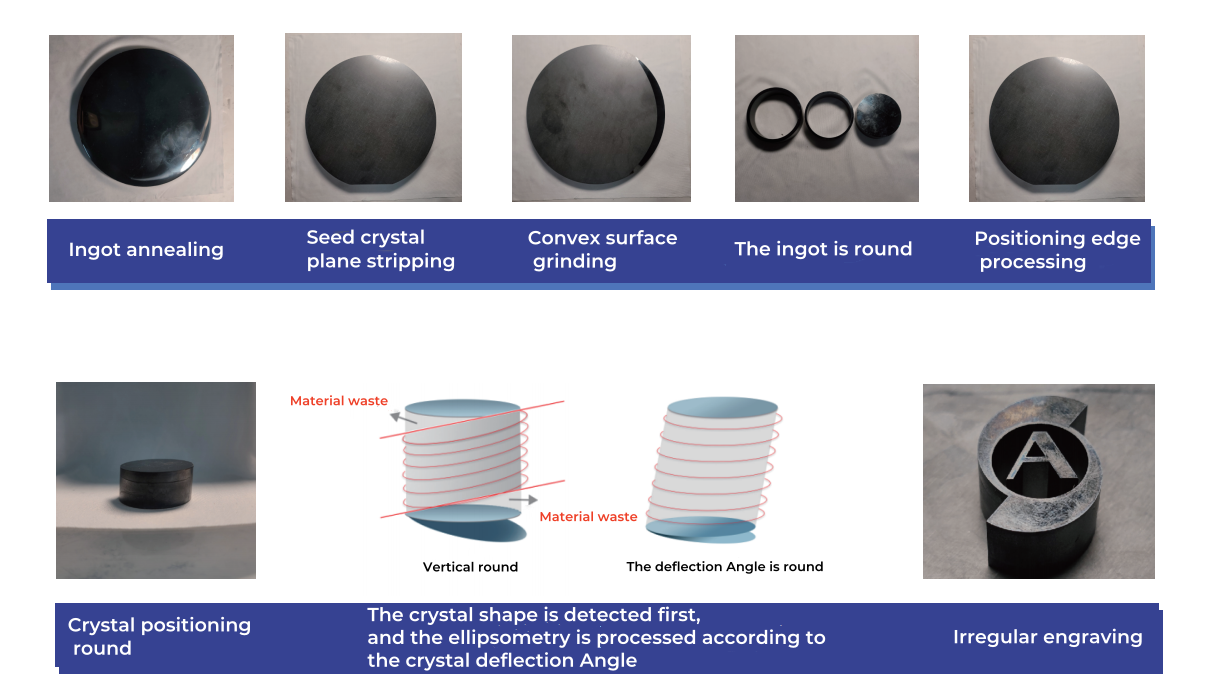
XKH's services:
XKH provides a full range of full life cycle service support for microjet laser technology equipment, from the early process development and equipment selection consultation, to the mid-term customized system integration (including the special matching of laser source, jet system and automation module), to the later operation and maintenance training and continuous process optimization, the whole process is equipped with professional technical team support; Based on 20 years of precision machining experience, we can provide one-stop solutions including equipment verification, mass production introduction and after-sales rapid response (24 hours of technical support + key spare parts reserve) for different industries such as semiconductor and medical, and promise 12 months long warranty and lifelong maintenance and upgrade service. Ensure that customer equipment always maintains industry-leading processing performance and stability.
Detailed Diagram
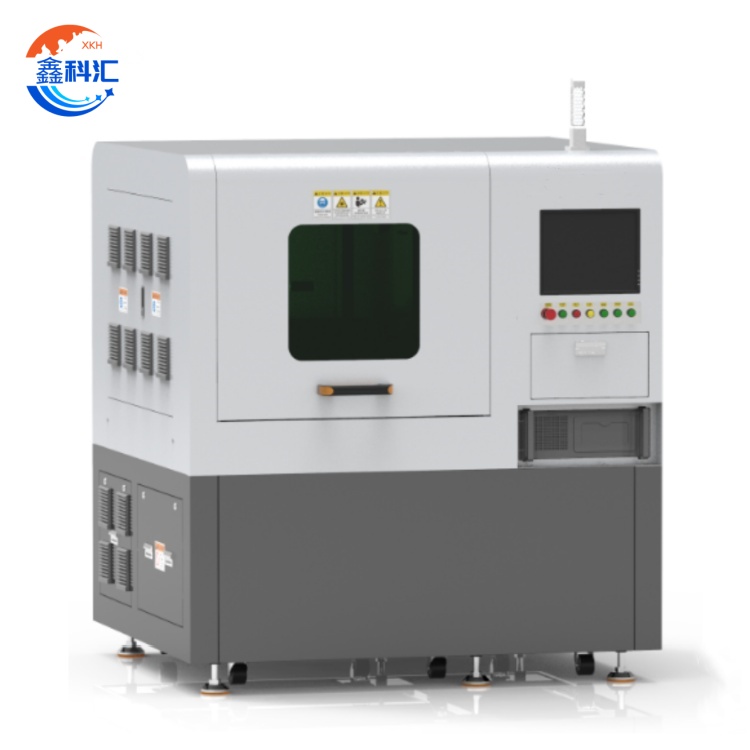
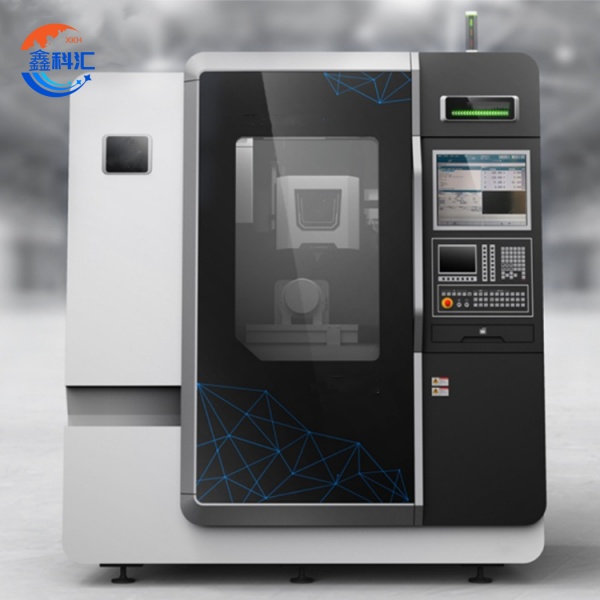
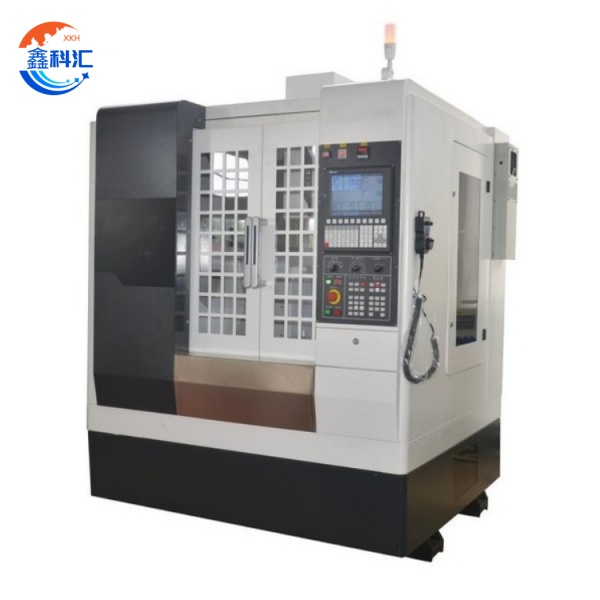