SiC ceramic tray plate graphite with CVD SiC coating for equipment
Silicon carbide ceramics are not only used in the thin film deposition stage, such as epitaxy or MOCVD, or in wafer processing, at the heart of which the wafer carrier trays for MOCVD are first subjected to the deposition environment, and are therefore highly resistant to heat and corrosion.SiC-coated carriers also have high thermal conductivity and excellent thermal distribution properties.
Pure Chemical Vapor Deposition Silicon Carbide (CVD SiC) wafer carriers for high temperature Metal Organic Chemical Vapor Deposition (MOCVD) processing.
Pure CVD SiC wafer carriers are significantly superior to the conventional wafer carriers used in this process, which are graphite and coated with a layer of CVD SiC. these coated graphite-based carriers cannot withstand the high temperatures (1100 to 1200 degrees Celsius) required for GaN deposition of today's high brightness blue and white led. The high temperatures cause the coating to develop tiny pinholes through which process chemicals erode the graphite beneath. The graphite particles then flake off and contaminate the GaN, causing the coated wafer carrier to be replaced.
CVD SiC has a purity of 99.999% or more and has high thermal conductivity and thermal shock resistance. Therefore, it can withstand the high temperatures and harsh environments of high brightness LED manufacturing. It is a solid monolithic material that reaches theoretical density, produces minimal particles, and exhibits very high corrosion and erosion resistance. The material can change opacity and conductivity without introducing metallic impurities. Wafer carriers are typically 17 inches in diameter and can hold up to 40 2-4 inch wafers.
Detailed Diagram
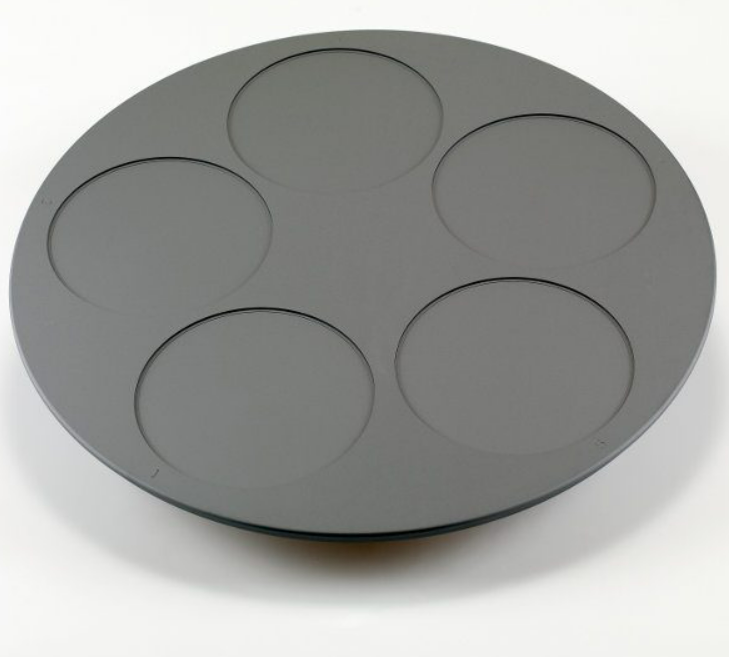
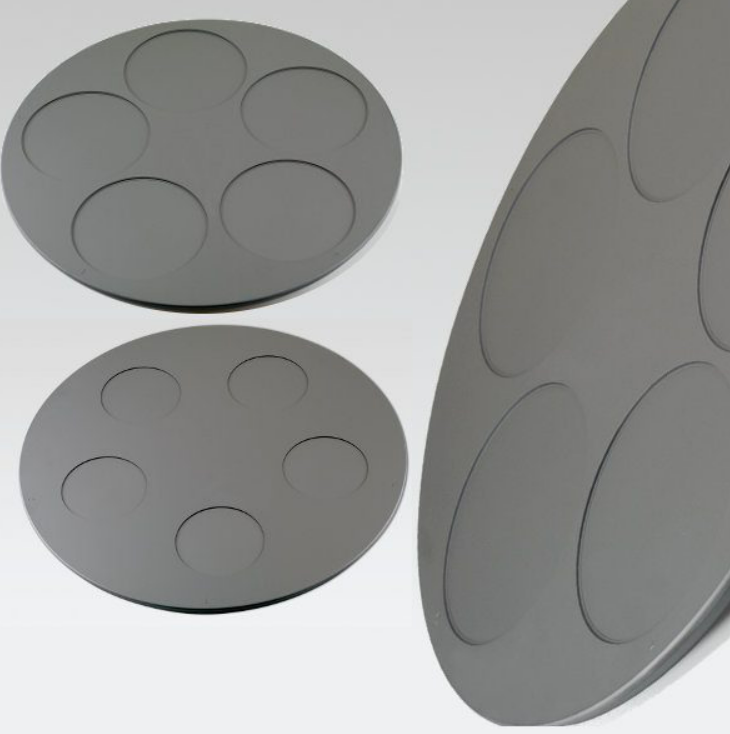
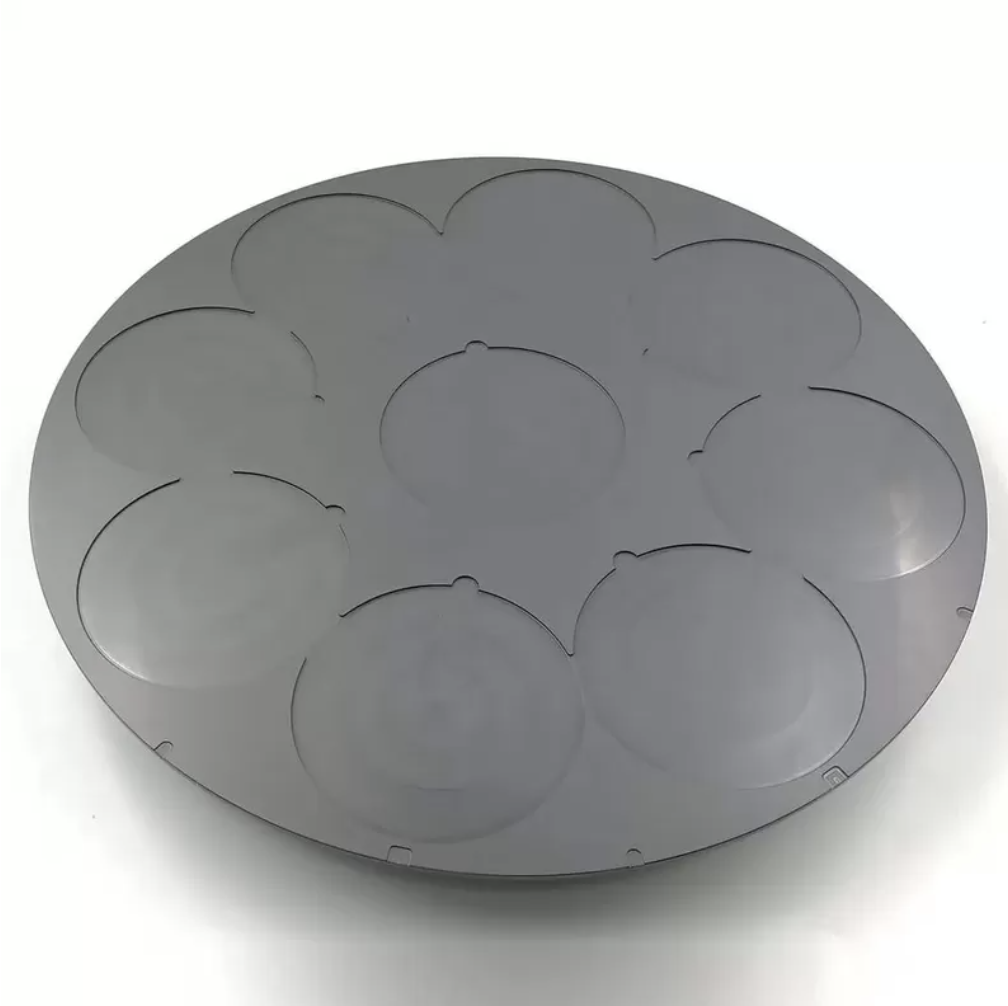