Silicon carbide diamond wire cutting machine 4/6/8/12 inch SiC ingot processing
Working principle:
1. Ingot fixation: SiC ingot (4H/6H-SiC) is fixed on the cutting platform through the fixture to ensure the position accuracy (±0.02mm).
2. Diamond line movement: diamond line (electroplated diamond particles on the surface) is driven by the guide wheel system for high-speed circulation (line speed 10~30m/s).
3. Cutting feed: the ingot is fed along the set direction, and the diamond line is cut simultaneously with multiple parallel lines (100~500 lines) to form multiple wafers.
4. Cooling and chip removal: Spray coolant (deionized water + additives) in the cutting area to reduce heat damage and remove chips.
Key parameters:
1. Cutting speed: 0.2~1.0mm/min (depending on the crystal direction and thickness of SiC).
2. Line tension: 20~50N (too high easy to break line, too low affect cutting accuracy).
3.Wafer thickness: standard 350~500μm, wafer can reach 100μm.
Main features:
(1) Cutting accuracy
Thickness tolerance: ±5μm (@350μm wafer), better than conventional mortar cutting (±20μm).
Surface roughness: Ra<0.5μm (no additional grinding required to reduce the amount of subsequent processing).
Warpage: <10μm (reduce the difficulty of subsequent polishing).
(2) Processing efficiency
Multi-line cutting: cutting 100~500 pieces at a time, increasing production capacity 3~5 times (vs. Single line cut).
Line life: The diamond line can cut 100~300km SiC (depending on the ingot hardness and process optimization).
(3) Low damage processing
Edge breakage: <15μm (traditional cutting >50μm), improve the wafer yield.
Subsurface damage layer: <5μm (reduce polishing removal).
(4) Environmental protection and economy
No mortar contamination: Reduced waste liquid disposal costs compared to mortar cutting.
Material utilization: Cutting loss <100μm/ cutter, saving SiC raw materials.
Cutting effect:
1. Wafer quality: no macroscopic cracks on the surface, few microscopic defects (controllable dislocation extension). Can directly enter the rough polishing link, shorten the process flow.
2. Consistency: the thickness deviation of the wafer in the batch is <±3%, suitable for automated production.
3.Applicability: Support 4H/6H-SiC ingot cutting, compatible with conductive/semi-insulated type.
Technical specification:
Specification | Details |
Dimensions (L × W × H) | 2500x2300x2500 or customize |
Processing material size range | 4, 6, 8, 10, 12 inches of silicon carbide |
Surface roughness | Ra≤0.3u |
Average cutting speed | 0.3mm/min |
Weight | 5.5t |
Cutting process setting steps | ≤30 steps |
Equipment noise | ≤80 dB |
Steel wire tension | 0~110N(0.25 wire tension is 45N) |
Steel wire speed | 0~30m/S |
Total power | 50kw |
Diamond wire diameter | ≥0.18mm |
End flatness | ≤0.05mm |
Cutting and breaking rate | ≤1%(except for human reasons, silicon material, line, maintenance and other reasons) |
XKH Services:
XKH provides the whole process service of silicon carbide diamond wire cutting machine, including equipment selection (wire diameter/wire speed matching), process development (cutting parameter optimization), consumables supply (diamond wire, guide wheel) and after-sales support (equipment maintenance, cutting quality analysis), to help customers achieve high yield (>95%), low cost SiC wafer mass production. It also offers customized upgrades (such as ultra-thin cutting, automated loading and unloading) with a 4-8 week lead time.
Detailed Diagram
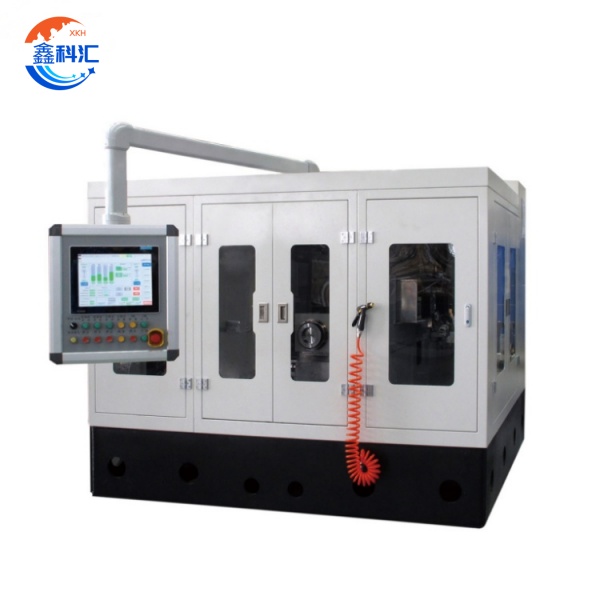
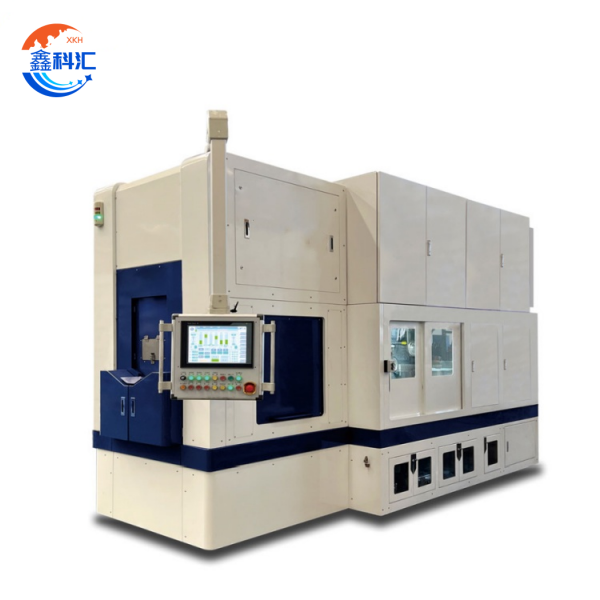
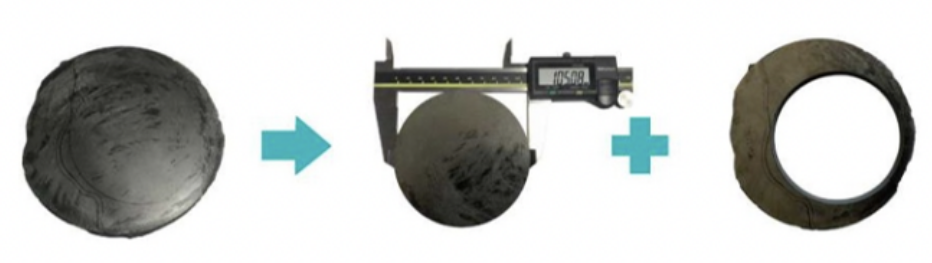