Silicon carbide resistance long crystal furnace growing 6/8/12inch inch SiC ingot crystal PVT method
Working principle:
1. Raw material loading: high purity SiC powder (or block) placed at the bottom of the graphite crucible (high temperature zone).
2. Vacuum/inert environment: vacuum the furnace chamber (<10⁻³ mbar) or pass inert gas (Ar).
3. High temperature sublimation: resistance heating to 2000~2500℃, SiC decomposition into Si, Si₂C, SiC₂ and other gas phase components.
4. Gas phase transmission: the temperature gradient drives the diffusion of the gas phase material to the low temperature region (seed end).
5. Crystal growth: The gas phase recrystallizes on the surface of the Seed Crystal and grows in a directional direction along the C-axis or A-axis.
Key parameters:
1. Temperature gradient: 20~50℃/cm (control growth rate and defect density).
2. Pressure: 1~100mbar (low pressure to reduce impurity incorporation).
3.Growth rate: 0.1~1mm/h (affecting crystal quality and production efficiency).
Main features:
(1) Crystal quality
Low defect density: microtubule density <1 cm⁻², dislocation density 10³~10⁴ cm⁻² (through seed optimization and process control).
Polycrystalline type control: can grow 4H-SiC (mainstream), 6H-SiC, 4H-SiC proportion >90% (need to accurately control the temperature gradient and gas phase stoichiometric ratio).
(2) Equipment performance
High temperature stability: graphite heating body temperature >2500℃, furnace body adopts multi-layer insulation design (such as graphite felt + water-cooled jacket).
Uniformity control: Axial/radial temperature fluctuations of ±5 ° C ensure crystal diameter consistency (6-inch substrate thickness deviation <5%).
Degree of automation: Integrated PLC control system, real-time monitoring of temperature, pressure and growth rate.
(3) Technological advantages
High material utilization: raw material conversion rate >70% (better than CVD method).
Large size compatibility: 6-inch mass production has been achieved, 8-inch is in the development stage.
(4) Energy consumption and cost
The energy consumption of a single furnace is 300~800kW·h, accounting for 40%~60% of the production cost of SiC substrate.
The equipment investment is high (1.5M 3M per unit), but the unit substrate cost is lower than the CVD method.
Core applications:
1. Power electronics: SiC MOSFET substrate for electric vehicle inverter and photovoltaic inverter.
2. Rf devices: 5G base station GaN-on-SiC epitaxial substrate (mainly 4H-SiC).
3. Extreme environment devices: high temperature and high pressure sensors for aerospace and nuclear energy equipment.
Technical parameters:
Specification | Details |
Dimensions (L × W × H) | 2500 × 2400 × 3456 mm or customize |
Crucible Diameter | 900 mm |
Ultimate Vacuum Pressure | 6 × 10⁻⁴ Pa (after 1.5h of vacuum) |
Leakage Rate | ≤5 Pa/12h (bake-out) |
Rotation Shaft Diameter | 50 mm |
Rotation Speed | 0.5–5 rpm |
Heating Method | Electric resistance heating |
Maximum Furnace Temperature | 2500°C |
Heating Power | 40 kW × 2 × 20 kW |
Temperature Measurement | Dual-color infrared pyrometer |
Temperature Range | 900–3000°C |
Temperature Accuracy | ±1°C |
Pressure Range | 1–700 mbar |
Pressure Control Accuracy | 1–10 mbar: ±0.5% F.S; 10–100 mbar: ±0.5% F.S; 100–700 mbar: ±0.5% F.S |
Operation Type | Bottom loading, manual/automatic safety options |
Optional Features | Dual temperature measurement, multiple heating zones |
XKH Services:
XKH provides the whole process service of SiC PVT furnace, including equipment customization (thermal field design, automatic control), process development (crystal shape control, defect optimization), technical training (operation and maintenance) and after-sales support (graphite parts replacement, thermal field calibration) to help customers achieve high-quality sic crystal mass production. We also provide process upgrade services to continuously improve crystal yield and growth efficiency, with a typical lead time of 3-6 months.
Detailed Diagram
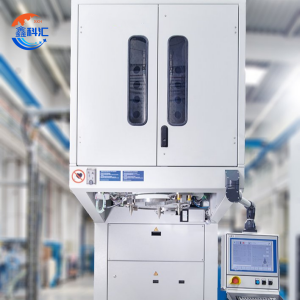
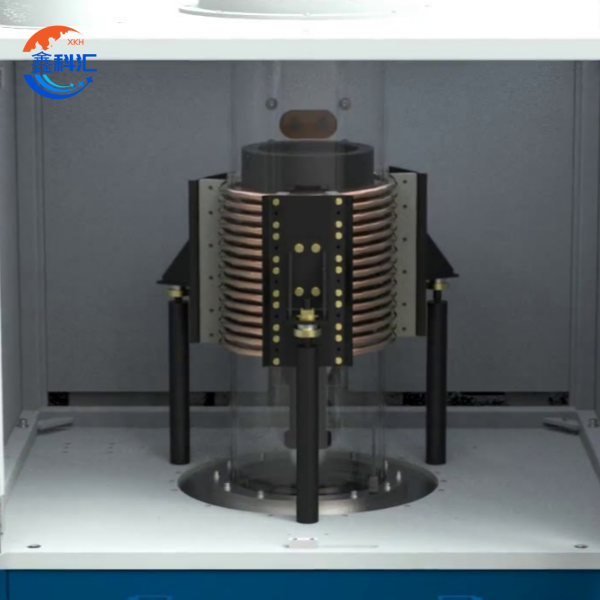
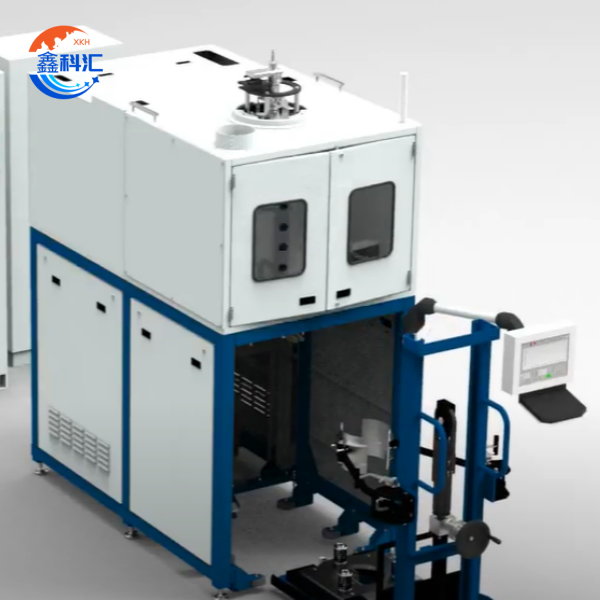